Hydraulic valve adjustment is a critical aspect of industrial systems that utilize hydraulic equipment. This adjustment ensures that the system operates optimally, with efficient performance and minimized risk of equipment failure. In this paper, we will provide a comprehensive understanding of hydraulic valve adjustment, its impacts when not performed correctly, best practices for performing hydraulic valve adjustment, the benefits of proper adjustment, and case studies of successful implementations.
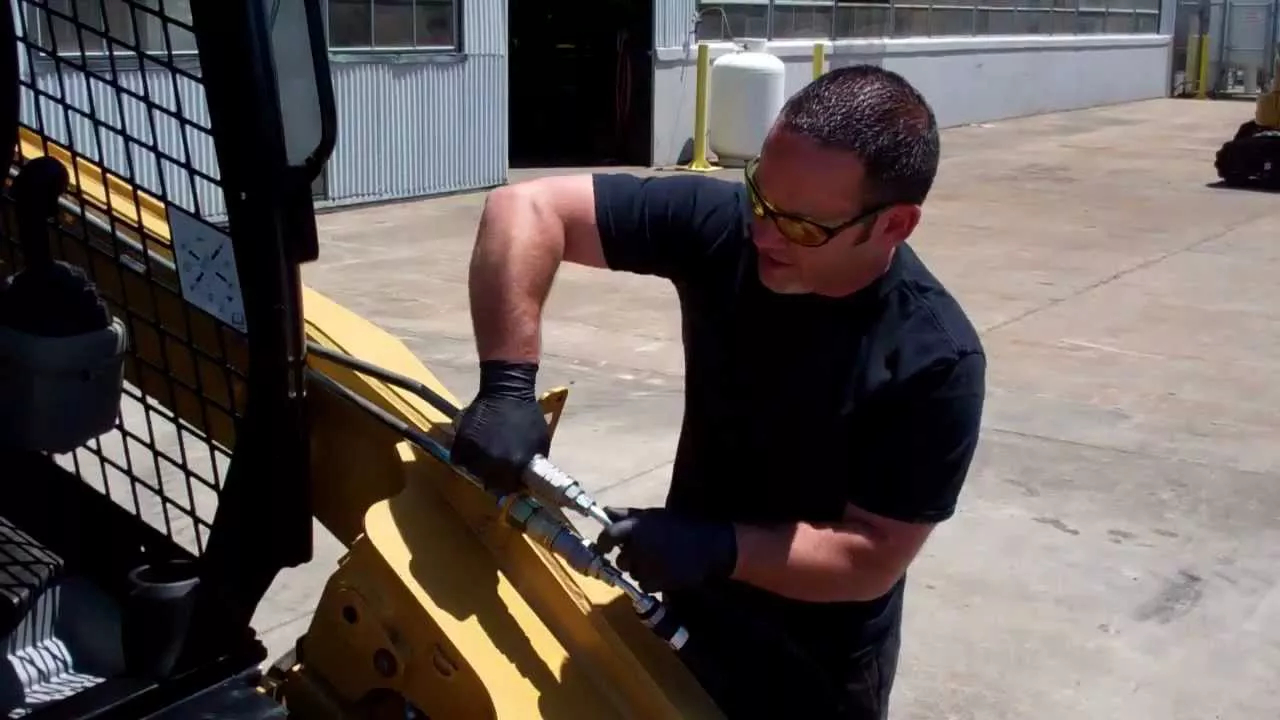
Proper hydraulic valve adjustment is crucial in ensuring that the equipment operates at peak efficiency. Hydraulic systems are essential in various industries, including manufacturing, construction, and transportation. A malfunctioning hydraulic system can cause significant equipment downtime and production delays, resulting in financial losses. Therefore, regular maintenance and inspection are necessary to ensure optimal hydraulic system performance. This paper aims to provide detailed insights into the importance of hydraulic valve adjustment and how it can be done correctly to achieve optimal system performance.
Understanding Hydraulic Valve Adjustment
Hydraulic valve adjustment is the process of adjusting the clearance between the valve and the rocker arm in a hydraulic system. The hydraulic valve adjustment system consists of several components, including the camshaft, lifters, pushrods, rocker arms, and valves. The adjustment ensures that the valve operates optimally by providing the correct amount of clearance between the valve and the rocker arm.
Proper hydraulic valve adjustment is crucial for several reasons. Firstly, it ensures that the system operates at peak efficiency by ensuring that the valves open and close at the correct times. If the clearance is not adjusted correctly, the valve may not open or close completely, resulting in reduced system efficiency. Secondly, it ensures that the system operates quietly by reducing the noise generated by the valve train. Lastly, proper adjustment ensures that the valve and other components do not experience premature wear and tear, which can lead to costly repairs.
Determining the need for hydraulic valve adjustment involves several methods. One of the most common methods is to listen to the engine for any unusual noises. If there is a tapping sound coming from the engine, it may indicate that the valve clearance needs adjustment. Another method involves checking the engine specifications and manufacturer’s recommendations for the recommended valve adjustment intervals. If the engine has been running for an extended period without adjustment, it may require adjustment to ensure optimal performance.
In conclusion, understanding hydraulic valve adjustment and its components is crucial in ensuring optimal system performance. Proper adjustment provides several benefits, including improved efficiency, reduced noise, and extended component lifespan. It is also essential to regularly inspect and maintain the hydraulic system to ensure that it operates optimally.
Impacts of Improper Hydraulic Valve Adjustment
Improper hydraulic valve adjustment can have significant impacts on system performance, efficiency, and safety. The following are some of the impacts of incorrect hydraulic valve adjustment:
- Reduced System Performance and Efficiency: When the valve clearance is not adjusted correctly, the valve may not open and close completely, resulting in reduced engine performance and efficiency. This can lead to decreased power output, lower fuel efficiency, and increased emissions.
- Increased Risk of Equipment Failure and Downtime: Improper hydraulic valve adjustment can cause premature wear and tear on the valve and other components, resulting in costly repairs or replacement. This can also cause unplanned equipment downtime, which can lead to production delays and financial losses.
- Safety Considerations: In some cases, incorrect hydraulic valve adjustment can result in safety hazards. For example, if the valve does not close completely, it can cause the engine to overheat or lead to oil leakage. This can pose a safety risk to operators and other personnel working in the vicinity of the equipment.
- Environmental Impact: Incorrect hydraulic valve adjustment can also lead to increased emissions, contributing to air pollution and negatively impacting the environment.
In conclusion, improper hydraulic valve adjustment can have significant impacts on system performance, efficiency, safety, and the environment. It is, therefore, essential to perform regular maintenance and inspection of the hydraulic system to ensure that it operates optimally and safely.
Best Practices for Hydraulic Valve Adjustment
Performing proper hydraulic valve adjustment requires a comprehensive understanding of the system’s requirements and specifications. The following are some best practices to ensure that hydraulic valve adjustment is done correctly:
- Understand System Requirements and Specifications: It is essential to understand the system’s requirements and specifications, including the manufacturer’s recommendations for valve clearance and adjustment intervals. This information can be found in the system manual or by contacting the manufacturer.
- Proper Use of Tools and Equipment: Using the correct tools and equipment is crucial in performing proper hydraulic valve adjustment. Ensure that the tools used are of high quality and designed specifically for hydraulic valve adjustment.
- Proper Adjustment Techniques: The adjustment process involves loosening the lock nut and adjusting the valve clearance using a feeler gauge. The valve clearance should be adjusted to the manufacturer’s recommended specifications. It is essential to ensure that the valve is fully closed before making any adjustments.
- Regular Maintenance and Inspection: Regular maintenance and inspection of the hydraulic system are necessary to ensure optimal performance. It is recommended to perform valve adjustment at regular intervals as specified by the manufacturer. Regular inspections can also help detect any issues early, preventing costly repairs or replacements.
- Follow Safety Procedures: Hydraulic systems can be dangerous, and safety procedures should always be followed. This includes wearing appropriate personal protective equipment, ensuring that the equipment is turned off before performing adjustments, and following all safety guidelines provided by the manufacturer.
In conclusion, following best practices for hydraulic valve adjustment can ensure that the system operates optimally, reducing the risk of equipment failure and downtime. It is essential to understand the system’s requirements, use the proper tools and equipment, follow proper adjustment techniques, perform regular maintenance and inspection, and follow safety procedures.
Benefits of Proper Hydraulic Valve Adjustment
Proper hydraulic valve adjustment provides several benefits, including improved system performance and efficiency, extended equipment lifespan, reduced maintenance needs, improved safety, and environmental performance. The following are some of the benefits of proper hydraulic valve adjustment:
- Improved System Performance and Efficiency: Proper hydraulic valve adjustment ensures that the system operates at peak efficiency, with valves opening and closing at the correct times. This improves the system’s overall performance and reduces fuel consumption, leading to cost savings.
- Extended Equipment Lifespan: Hydraulic equipment is expensive, and premature wear and tear can result in costly repairs or replacements. Proper hydraulic valve adjustment ensures that the equipment operates optimally, reducing the risk of premature wear and tear and extending its lifespan.
- Reduced Maintenance Needs: Regular maintenance and inspection are necessary to ensure optimal hydraulic system performance. Proper hydraulic valve adjustment reduces the need for costly repairs and maintenance, saving time and money in the long run.
- Improved Safety and Environmental Performance: Proper hydraulic valve adjustment reduces the risk of safety hazards, such as overheating or oil leakage, leading to improved safety for operators and other personnel working in the vicinity of the equipment. Proper adjustment also leads to reduced emissions, contributing to a cleaner environment.

In conclusion, proper hydraulic valve adjustment provides several benefits, including improved system performance and efficiency, extended equipment lifespan, reduced maintenance needs, improved safety, and environmental performance. It is essential to follow best practices for hydraulic valve adjustment to ensure that the system operates optimally and safely, leading to cost savings and improved performance.
Case Studies
Several case studies have demonstrated the benefits of proper hydraulic valve adjustment. The following are examples of successful implementations and their outcomes:
John Deere Tractor Hydraulics Troubleshooting 2950
- Case Study 1: A manufacturing company noticed that their hydraulic system was experiencing reduced performance and increased noise levels. Upon inspection, it was determined that the hydraulic valve clearance needed adjustment. After performing the adjustment, the system’s performance and efficiency improved, and the noise levels reduced significantly. The company reported cost savings due to reduced fuel consumption and reduced maintenance needs.
- Case Study 2: A construction company was experiencing frequent equipment downtime due to hydraulic system failures. After inspecting the system, it was determined that the valve clearance needed adjustment. The adjustment was performed, and the equipment downtime reduced significantly. The company reported cost savings due to reduced equipment downtime and maintenance needs.
- Case Study 3: A transportation company noticed increased emissions and reduced fuel efficiency in their fleet. Upon inspection, it was determined that the hydraulic valve clearance needed adjustment. After performing the adjustment, the fleet’s emissions reduced, and fuel efficiency improved, leading to cost savings and improved environmental performance.
These case studies demonstrate the benefits of proper hydraulic valve adjustment, including improved system performance and efficiency, reduced maintenance needs, and cost savings. Regular maintenance and inspection, including hydraulic valve adjustment, can lead to significant cost savings and improved system performance.
In conclusion, case studies have demonstrated the positive impacts of proper hydraulic valve adjustment on system performance, efficiency, and cost savings. Implementing best practices for hydraulic valve adjustment can lead to improved equipment lifespan, reduced maintenance needs, and improved environmental performance.
Conclusion
In conclusion, hydraulic valve adjustment is a critical aspect of industrial systems that utilize hydraulic equipment. Proper adjustment ensures optimal system performance, extended equipment lifespan, reduced maintenance needs, improved safety, and environmental performance. Improper adjustment can lead to reduced system performance and efficiency, increased risk of equipment failure and downtime, safety hazards, and environmental impact.
Best practices for hydraulic valve adjustment include understanding system requirements and specifications, using proper tools and equipment, following proper adjustment techniques, performing regular maintenance and inspection, and following safety procedures. Implementing these best practices can lead to improved system performance, reduced maintenance needs, and cost savings.
Understanding Hydraulic Pumps: How They Work and Their Applications
Case studies have demonstrated the benefits of proper hydraulic valve adjustment, including improved system performance and efficiency, reduced maintenance needs, and cost savings. It is, therefore, essential for industrial systems that utilize hydraulic equipment to prioritize proper hydraulic valve adjustment as part of their regular maintenance and inspection procedures.

In conclusion, the importance of proper hydraulic valve adjustment cannot be overstated. Implementing best practices for hydraulic valve adjustment can lead to improved system performance, extended equipment lifespan, reduced maintenance needs, improved safety, and environmental performance. We call upon all industrial systems that utilize hydraulic equipment to prioritize proper hydraulic valve adjustment for optimal system performance and safety.